Our Cutlass wagon needs floor pans.
Front and rear on both sides are pretty much shot, trans tunnel is good, so it looks like doing the complete left and right pans might be the best option.
Obviously DIY is cheaper, but how difficult of a project is this going to be? I'm a quick learner, I've done complete axle swaps, top end rebuilds, etc.. without experience or outside help.
I'm just really green when it comes to welding. My experience is limited to goofing around with a $99 Harbor Freight flux core arc welder.From what I've read, MIG is the way to go.
Can a newbie tackle a project like this?
I don't have a 220 line here, will a 110 MIG be adequate?
Aside from the MIG setup, clamps, and holding magnets, I have all the other necessary tools.
Thanks in advance.
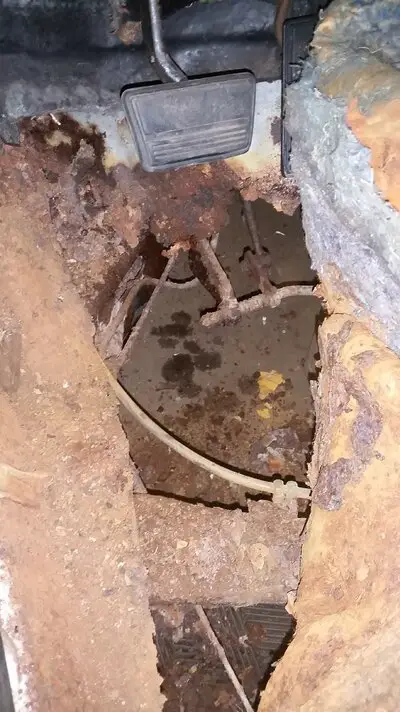
Front and rear on both sides are pretty much shot, trans tunnel is good, so it looks like doing the complete left and right pans might be the best option.
Obviously DIY is cheaper, but how difficult of a project is this going to be? I'm a quick learner, I've done complete axle swaps, top end rebuilds, etc.. without experience or outside help.
I'm just really green when it comes to welding. My experience is limited to goofing around with a $99 Harbor Freight flux core arc welder.From what I've read, MIG is the way to go.
Can a newbie tackle a project like this?
I don't have a 220 line here, will a 110 MIG be adequate?
Aside from the MIG setup, clamps, and holding magnets, I have all the other necessary tools.
Thanks in advance.
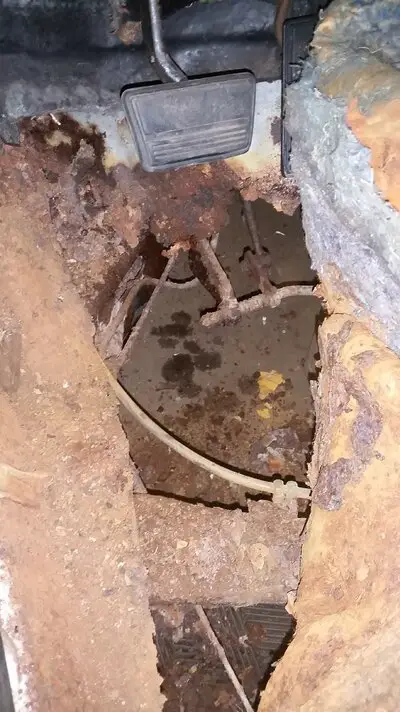